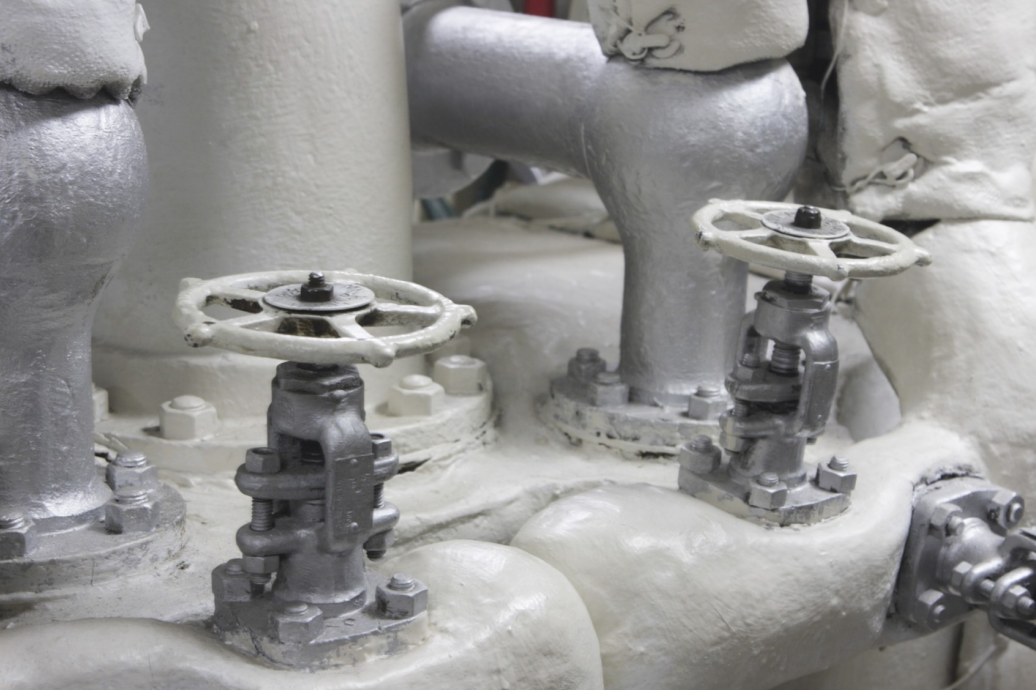
The Risk of Scalding and Serious Injury when Working on Steam Systems
Loss Prevention
Crewmembers can be badly scalded while working
on steam systems.
The following examples
illustrate how personnel have
been injured as a result of
either not following the correct
procedures or abiding by best
practice, or where they were
unaware of the work activities
of other crewmembers, with
disastrous consequences
Dmitry Kisil
(Senior Loss Prevention Officer, West P&I)
Incident One – Not following correct procedures:
Two engineers were injured while carrying out routine maintenance on a boiler. The engineers opened an inspection door and were scalded, one of them severely, by a violent escape of steam. Initial investigations revealed that the incident was due to human error rather than equipment failure as neither officer had followed the applicable procedures nor checked that the boiler had been de-pressurised prior to commencing the inspection.
Incident Two – Assumptions can lead to accidents:
Both men were badly scalded by the released steam and were hospitalised. One of them also sustained serious leg injuries after being struck by the valve bonnet and handwheel assembly.
It was later found that the steam line had not been isolated, de-pressurised or SA 008 drained. No checks were carried out as it was wrongly assumed that the engineer on the preceding watch had carried out this task. Furthermore, rather than slackening the nuts holding down the valve bonnet as a precaution, they were removed completely before the valve was loosened.
Incident Three – Poor interdepartmental communication:
A Class survey of a boiler was being undertaken in port. The vessel’s engineers were unaware that the Bosun and a deck rating were painting the exhaust pipes on top of the funnel casing. During the Class survey the attending surveyor asked for the boiler over-pressure safety vent valves to be tested.
The steam pressure in the boiler was increased until the safety vent valves tripped. The steam vented through an open ended pipe situated on top of the funnel casing which directed the flow towards the centre of the funnel top, scalding the rating severely.
The Bosun, standing on a small raised platform by the side of the vent, was blown onto the top deck of the funnel by the force of the blast, but escaped injury.
Subsequent investigations found that there was little communication between the deck and engine departments with regard to their respective work programmes. Moreover, the vent pipe was unmarked and crewmembers did not know that pressurised steam might escape at any time.
Conclusion
All involved in the operation should be refamiliarised with the applicable procedures and it may also be prudent to carry out a risk assessment beforehand. As a minimum the system should be de-pressurised, drained, cooled and isolated, and warning signs posted. Isolation valves should be locked or tied shut to prevent any backflow of steam or condensate, and blanking plates may also need to be inserted.
After emptying a boiler, care should be taken to check that the vacuum has been broken before the manhole doors are removed. Although an air cock may have been opened to break the vacuum, the manhole door nuts should be loosened and the joint broken before the dogs are released. The top manhole doors should be removed first, and personnel should stand well clear when the doors are opened in case of hot vapour. All departments should be kept informed throughout.
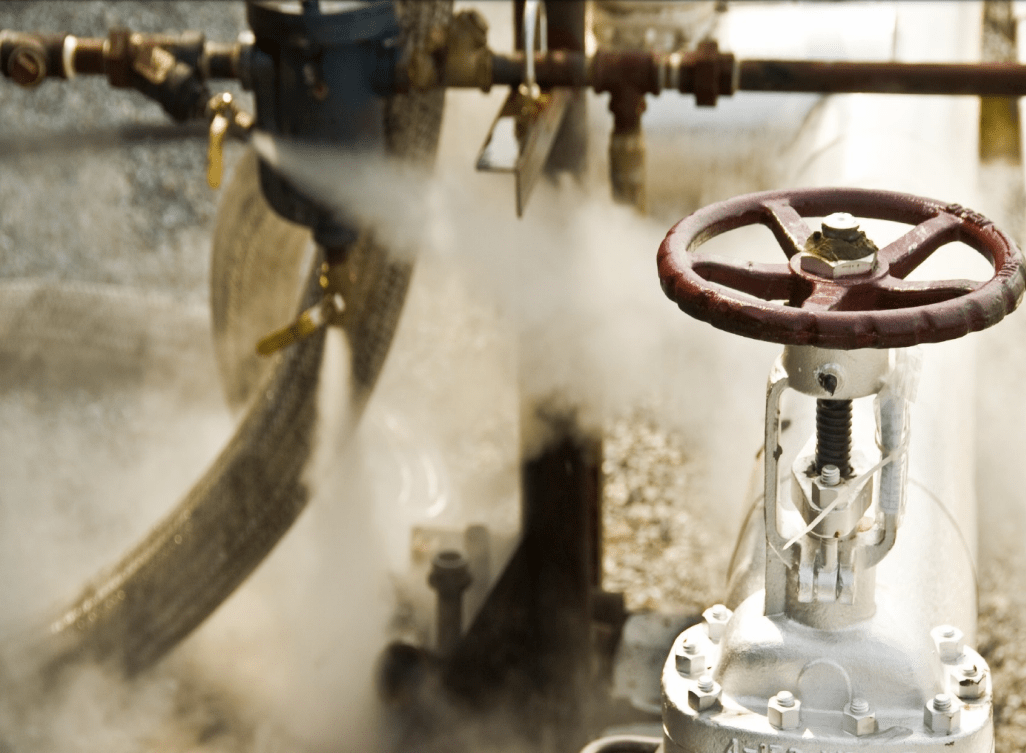
Members requiring further guidance on this topic should contact the Loss Prevention department.
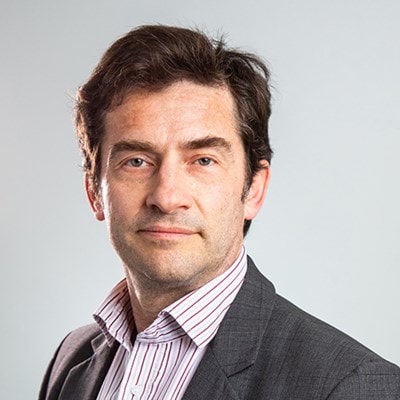
Dmitry is a qualified Marine Engineer and has an MBA in Shipping and Logistics. Having finished his seagoing service as a Chief Engineer, he worked as a Technical Superintendent and a Fleet Manager for a ship management company in London. Dmitry joined the Club in 2013 and attends to Condition Surveys and other Loss Prevention matters.