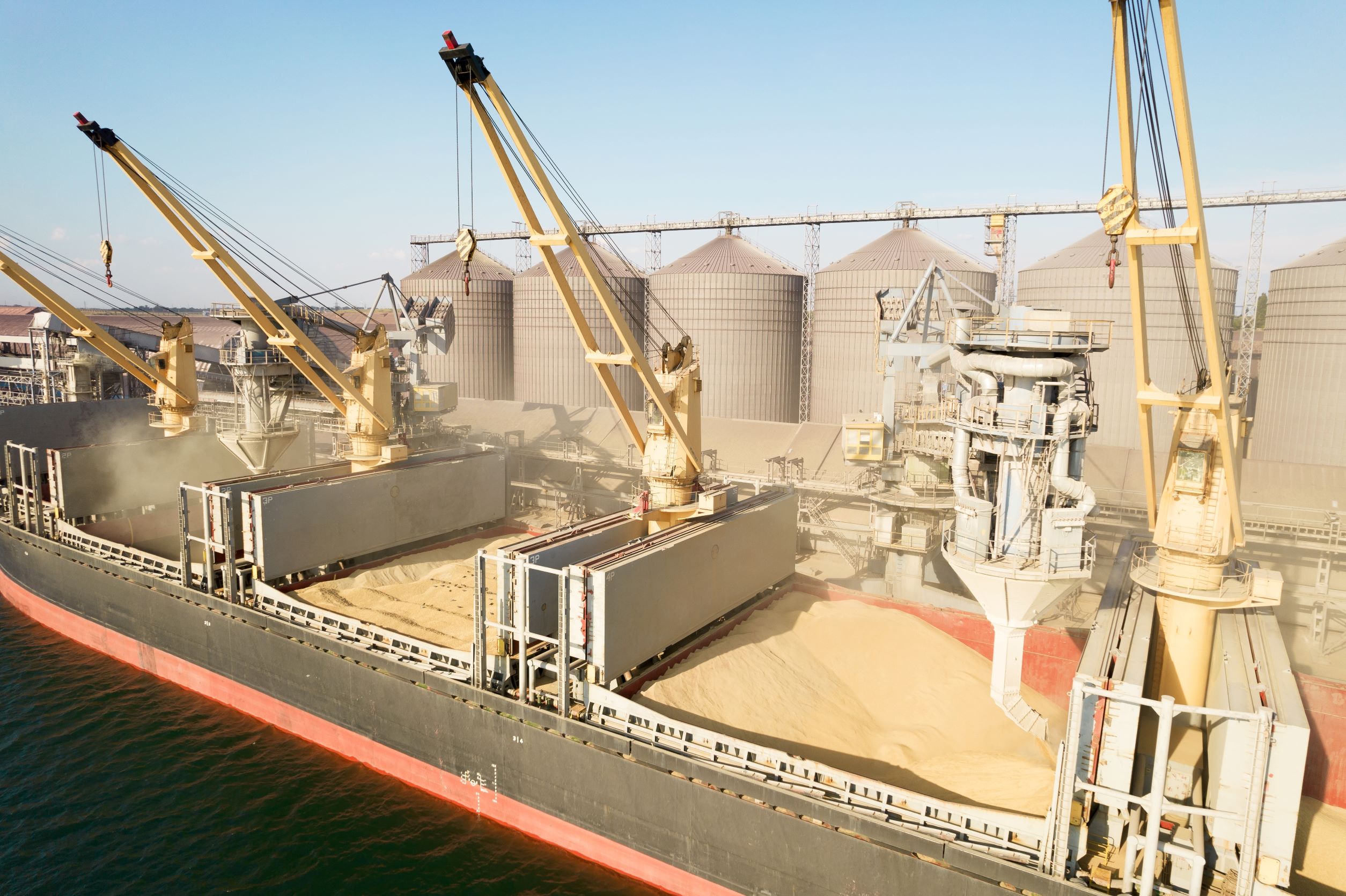
Crane Slewing Gear Maintenance and Rocking Tests
Loss Prevention Bulletin
Incidents continue due to pedestal crane slewing gear’s failure because of bearing wear, often leading to damage to equipment, cargo, significant repair delays and in events of catastrophic bearing failures, severe injury and fatalities. In many cases, the bearings fail with hook loads well below the crane’s safe working load.
Dean Crossley
(Loss Prevention Manager, West P&I)
The slewing ring attached to the rotating crane body will be subject to the most wear at the rear of the crane body opposite the jib and under the jib itself, the former being subject to tension and the latter to compression caused by the weight of the jib and loads suspended from the hook.
The principal causes leading to failure of a crane slewing ring bearings are lack of lubrication of the bearings and inadequate monitoring of the bearing wear down. Crane slewing ring bearing failure seems to affect single ball race type bearing arrangements principally; however, double ball race and roller bearings are also susceptible.
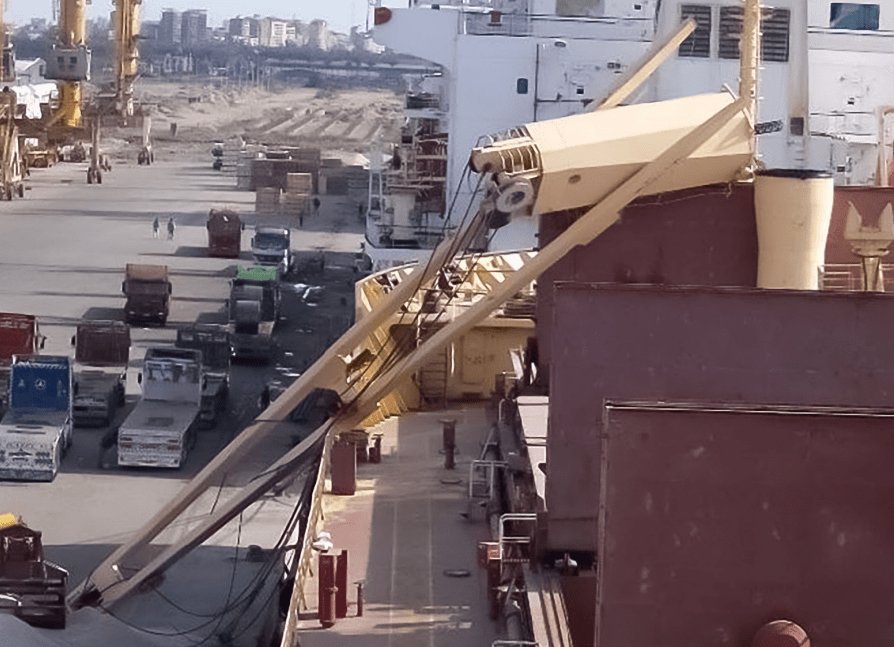
Greasing
A lack of lubrication accelerates bearing wear and corrosion; therefore, the inclusion of regular greasing within a vessel’s planned maintenance system is essential. The greasing interval will depend on the crane’s usage and the crane’s exposure to wet or dusty conditions, high humidity or extremes of temperature; for example, cranes located forward subject to increased exposure to sea spray will require more frequent greasing.
The crane manufacturer’s recommendations should be consulted when determining the greasing interval for a particular vessel. Grease should be injected into each grease nipple in turn whilst rotating the crane until a bead of fresh grease is sighted extruding from the grease seals’ lip. Any damaged or blocked grease nipples noted must be replaced . Manufacturers will generally specify the minimum quantity of grease to be applied, depending on the bearing’s size, over a specific length of time to ensure periodic renewal of all the grease. Additionally, greasing of the slewing rings after long periods of inactively should be completed.
In line with manufacturers’
recommendations, the correct grease
must be used; for example, grease containing Molybdenum Polysulphide
(MS2) can cause the bearings to
slide rather than roll in some slewing
ring types, increasing the wear rate.
Excessive old grease emanating from
sealing rings must be removed and
disposed of in line with regulatory
requirements to prevent it from falling
onto the main deck or external crane
ladders, creating a slip hazard.
In conjunction with the planned
periodic greasing of the slewing ring
bearing, the inner slewing ring open
gearing and slewing pinion should
also be dressed with the crane
manufacturer’s recommended grease
product, applied either by brush or
careful spraying. Excess used and
old grease should be removed and
disposed of properly.
Monitoring of Bearing Wear
Grease Analysis
Some manufacturers recommend that a representative sample of grease be extracted from four equidistant points on the slewing ring at periodic intervals and sent for analysis to assess the bearings’ condition.
Some slew rings have sampling ports fittings; this involves removing a bolt and drawing a grease sample from close to the bearing surface using a suitable syringe. If there are no sampling ports fitted, clean the outer seal next to the grease nipples closest to the four sampling locations; grease should be pumped into each grease nipple in turn without rotating the crane and the old grease expelled from the seal taken for analysis.
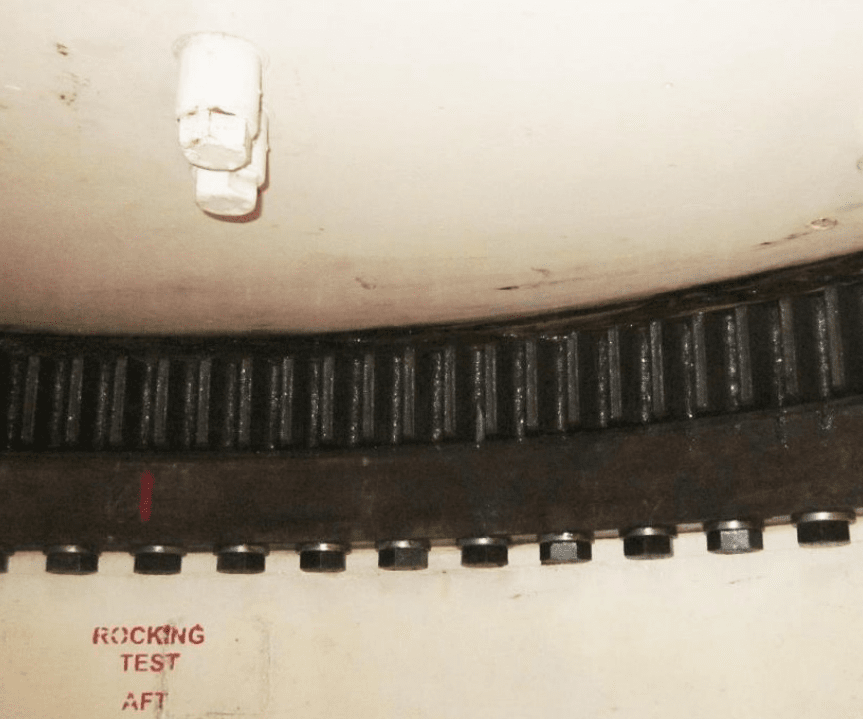
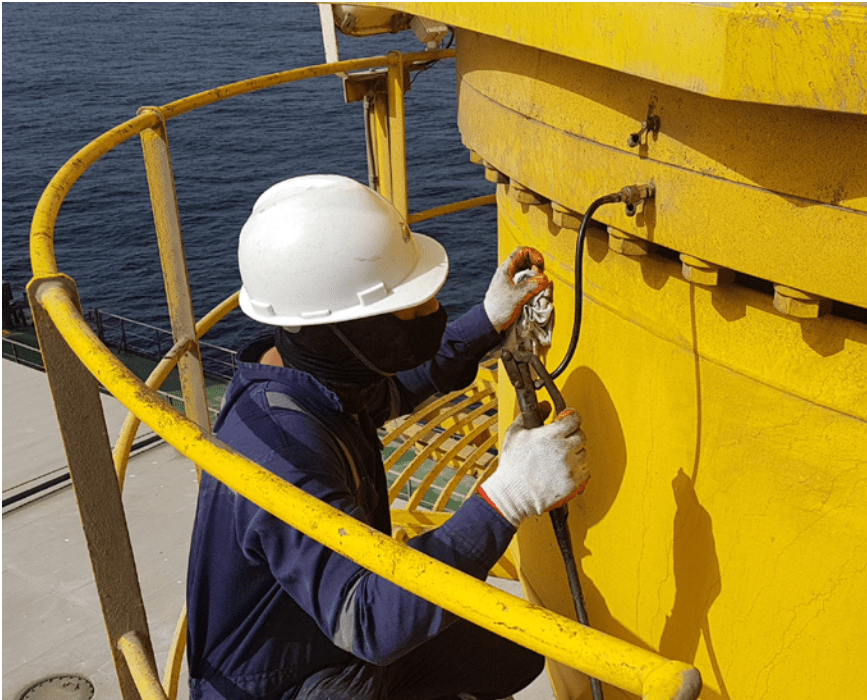
Rocking Test
To ensure that slewing ring bearings
are not becoming worn, the vessel’s
planned maintenance system should
include a rocking test, and each crane
tested every six months. A record of
these tests must be entered into the
Registry of Lifting Appliances.
The rocking test comprises the
measurement of the deflection
between the crane pedestal and the
rotating crane housing in the way of the
slewing ring using a dial test indicator
to determine the bearing clearances.
Measurements are taken at the
two locations on the slewing ring
susceptible to the most significant
bearing wear, under the jib’s centre
and diametrically opposite. A set of
eight readings are taken with the crane
pointing dead ahead, dead astern, to
port and then to starboard, initially with
the jib luffed to its minimum radius with
no weight on the hook and then with
the jib luffed to its maximum radius
with the difference between the two
readings giving the bearing clearance.
The readings are compared against the manufacturer’s maximum permissible clearance, which will depend on the type and size of the slewing ring and bearing size. The original bearing clearances should be available to determine the degree of wear. Consider shortening the testing intervals when the noted wear has increased appreciably between consecutive rocking tests.
Some manufacturers have produced integrated devices to measure unacceptable wear of the bearing in their slewing rings to provide early warning of excessive bearing wear.
During the five-year proof load testing and thorough annual examinations of lifting gear, a vessel’s Classification Society may require evidence showing that tests to determine bearing wear have been conducted together with results that show these are within the manufacturers’ limits. Neglecting these tests may result in the Classification Society not certifying the crane for further use.
Additional Concerns
It is also often found that the bolts’ torque settings holding the slewing bearing parts to the crane pedestal and crane body are not periodically checked in line with manufacturers’ recommendations. Therefore, in addition to routine maintenance and inspection of the slewing ring bearing, the bolts securing the slew ring’s inner and outer race should be examined, and their tightening torque periodically checked in line with manufacturers’ recommendations. The interval between successive checks will vary from manufacturer to manufacturer and usually is every twelve months; however, it may be as frequent as every three months.
Another potential oversight that can occur when it comes to the slew ring bearing bolts is the availability of certified testing facilities that can perform non-destructive testing on the bolts removed before the crane’s five-year proof testing. The quantity of slew ring bearing bolts required for removal to undergo the nondestructive testing will be based on the crane’s age, and this determines what percentage of bolts to remove from the slew ring bearing arrangement. When choosing which bolts are to be taken for examination, these must be from the slew ring bearing’s most highly loaded area.
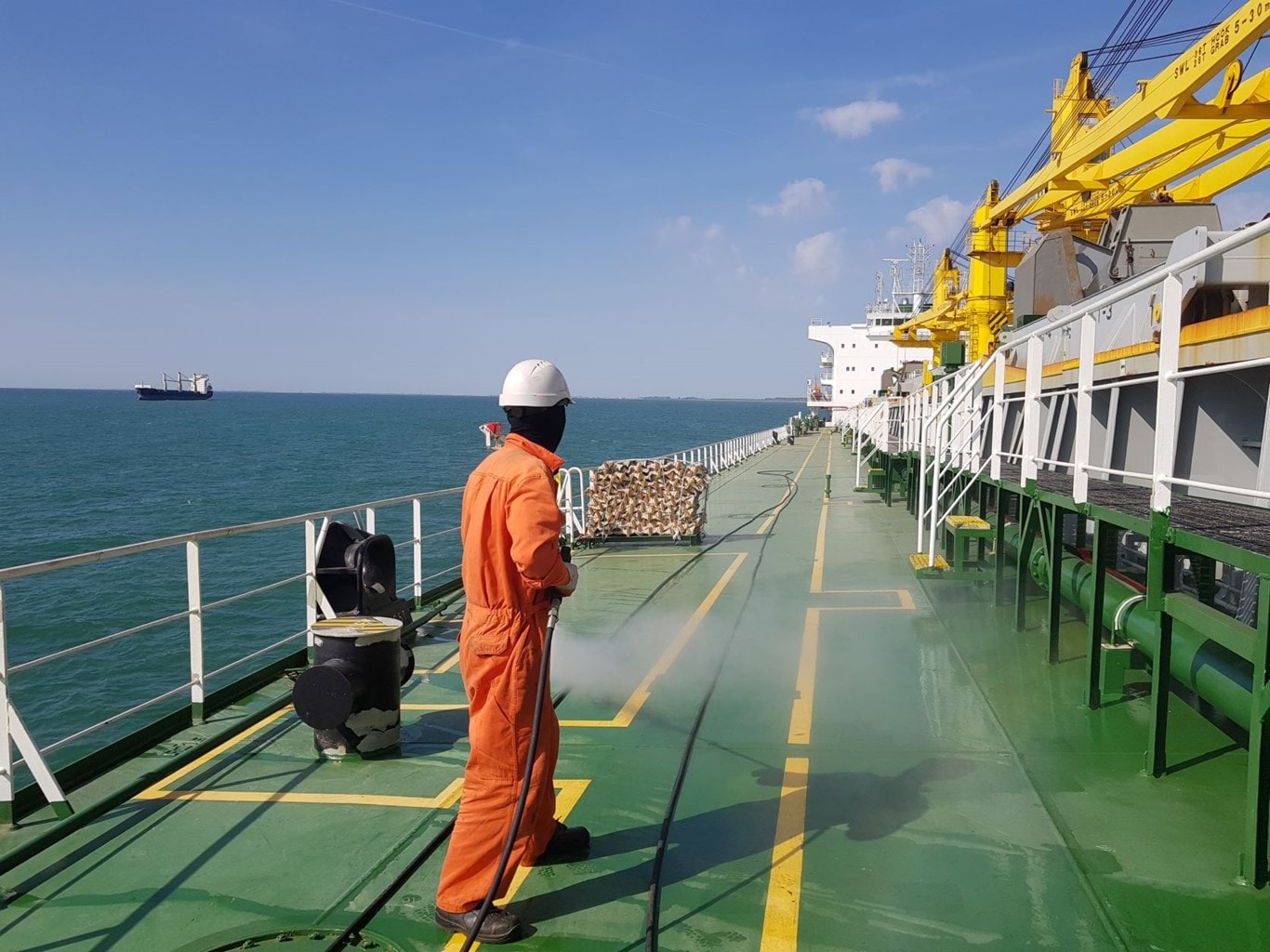
Members requiring any further guidance are advised to contact the Loss Prevention department.
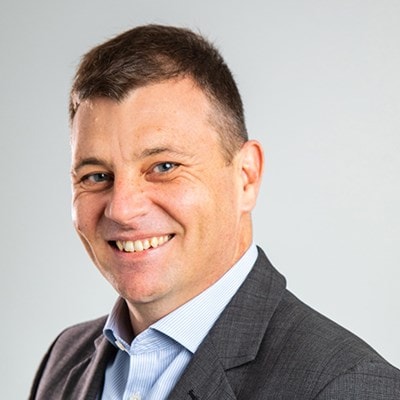
Dean Crossley
Loss Prevention Manager
T +44 20 7716 6059
E Dean.Crossley@westpandi.com
Dean is the Loss Prevention Manager at West P&I's London Office. He is a Master Mariner with seagoing experience on a variety of dry cargo vessel types. Before joining the Club in 2016, upon transferring to shore-based employment, for over 13 years, Dean has worked at an IG P&I Club in London as a Claims Manager and as a Marine & Warranty Surveyor at leading marine consultancies.